First is the forge

Steel frame, the main body is an old cast-iron sink; I cut a hole near one end and set in a brake drum as a firepot.
There's a hole cut at each end of the body so long pieces can be put in. Below is an angle of steel pipe with a squirrel-cage fan for the blower. Speed is controlled by a ceiling fan control; it works well. Below the forge is a: a bucket full of I don't remember(need to clean that out), b: water bucket for cooling hot things, and c: that yellow thing is an old air tank with one end cut off; for quenching things like double-edged blades I fill it with oil and use it. Please ignore the mess around it.
Next is the anvil
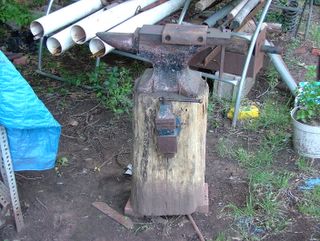
This one weighs 110 lbs. The piece sitting on top is a cutting saddle; a piece of mild steel bent to fit over(so it won't fall off), it's for chisel work such as cutting/splitting stock so you don't ding up the anvil face or your chisels. Sitting on a stump, which is on bricks to keep it off the ground when not in use. There's a small bench vise bolted to the stump, which has been hugely handy over time. A good anvil will have a hardened face, and if you're looking at one and you're not sure the easiest test is this: take a hammer, a small one will do, hold it about 6-8" above the face, and drop it. No, don't turn loose of the handle. If the face is hardened, the hammer will dance nicely, bouncing a few times; if it goes 'clunk' and sits there, don't buy it. You can't go by the sound, as I've seen fine anvils that rang like a bell(this one does) and others that just give a metallic 'thunk', so look for the bounce.
And for God's sake, don't just beat on the anvil without something to cushion it, like the piece you're forging. You'll have two pieces of hardened steel banging into each other, and bad things can happen, especially around the edge; hard strikes there with nothing to cushion them can chip and crack the edge of the face. And if you find a good one and the edges are sharp, I would suggest you get a belt sander and round them off. Doesn't have to be much, and it'll keep you from dinging the hammer face, as well as reducing the chance of knocking off chips. This one has a curve of between 1/4" up near the horn, getting smaller as you move toward the heel, and it took a while to grind it on.
In the future I'll post some pictures of various tools used on/with the above.
No comments:
Post a Comment