Most modern knives have the edge end before the blade meets the guard; in most old knives, continuing up into the 1800's, the edge came all the way back. If you want the ricasso to have a squared-off or rounded section before the guard, have the edge run back a little further than the point you want it to end, then make sure the area you want for the ricasso is square with the blade shape- not bent up or down. Remember, leave it a little big in all dimensions, especially to the rear.
Now comes the tang. If you want a full tang- as wide and long as the grips, which will be riveted or pinned on- it's fairly simple. Mark off a touch shorter than you want the tang to be and cut the piece off, then into the fire with that end. Unless your blade is quite long, you'll need tongs to hold onto the piece at this point. Bring the tang section up to heat and hammer it out. At this point do two things; leave it oversize in width and length, and taper it a bit in thickness. A tapered tang is just as strong, and a lot lighter.
If you want a narrow or 'stick' tang, you will need something like this:
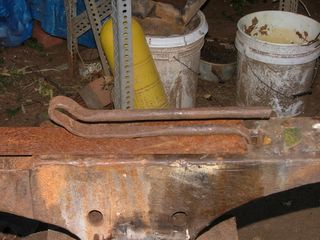
That piece on top of the anvil is a spring fuller. A fuller is a piece, often looking like a straight-peen hammer, used to shape a notch in steel. Often they're used as a set; the top fuller has a handle, the bottom fits into the hardy hole(the square one on the anvil face), and a hot piece is set between them to narrow it at that point. Obviously you need help to do it that way, so you can make one like this to do it alone. This is just a piece of coil spring from a truck suspension. Straighten out about two feet of it; flatten and bend one end into a 'U' to fit snugly into the hardy hole; flatten a section in the center and bend it over, leaving about an inch between the two round sections. To use it, you heat the area you wish to shape, slide it between the two round arms, and swat it right above the stock with a fairly heavy hammer. With a light piece you can use a lighter hammer, with a piece of thick stock you'll need more energy in the stroke. If the blade is very wide you put it in sideways, then turn it vertical. Pick a spot a little further back than you want the tang to begin(you can always grind up to the line), mark it if need be, heat it, put it in place and strike. Do one or two strokes, then flip the piece over and hit one or two from the other side; again, stop when the notches leave the stock a little wider than the finished tang will be. Now you can put the tang section back to heat, remove the fuller, and work out the tang.
Set the piece with the tang section on the anvil face and the notch at the edge, and hammer it along the length of the section; turn over and work the other side. That'll narrow and thicken it, so the next heat you work the sides, to thin and stretch the tang. Alternate sides to keep it even, and make the tang longer than needed. If you have a straight-peen hammer(cross-peen will do, straight is easier for me), you can use it like this: use the peen side and hammer a set of parallel notches in the piece, then flip it over and do the same, then flip back and flatten with the regular face. This will stretch the piece a lot faster, but if you don't watch it you can wind up making it thinner than you planned; it takes practice.
When the tang is forged, look at the piece from all angles. Is it straight? Is it twisted anywhere along its' length? Is the edge centered? If you spot a problem, correct it now, striking- or bending or twisting- just hard enough. When all is ready, there's a last step I'd recommend, called packing.
Supposedly this can refine the structure of the steel, making a better blade; I have noticed that if I do it right, it does seem to make a difference. Without that factor, it does smooth and even up the surface. In any case, take a hammer with a smooth face- not flat, just slightly rounded and as wide as you have-, bring as much of the blade as possible up to a low red heat, lay it on the anvil face with the flat of one side on the face, and start hammering with light, fast blows. Remember, this is not to shape, this is to refine, so control yourself. After it cools to a dark red, heat it back up and do the same on the other side, and try to use the same number of blows(roughly) and cover the same area as the first heat. If you need to heat a long blade in sections, no problem, just keep it even.
When you're done with this, back to the fire. This time you need to get the whole blade, or as much of it as you can, to a low red heat, as evenly over the length as possible. When it's there, take it out and let it cool in the air. I'll often clamp the tang in a vise and let it sit if it's a big one. When it's dark, do it again. I generally go for three annealing heats like this, the purpose of which is to even out stresses from hammering and, if you got it a bit too hot in earlier stages, will help keep the grain size of the steel where it should be. After the third heat, clamp it in the vise or set it somewhere safe and let it cool down completely.
The forging is done at this point. Next comes grinding, then heat-treating, then polishing.
No comments:
Post a Comment